Greetings!
As this is my first post here, allow me to introduce my self - Jeff from Pensacola. Like Grant, I mostly do ships. Here's a pic of my last ship - the English ship revenge.
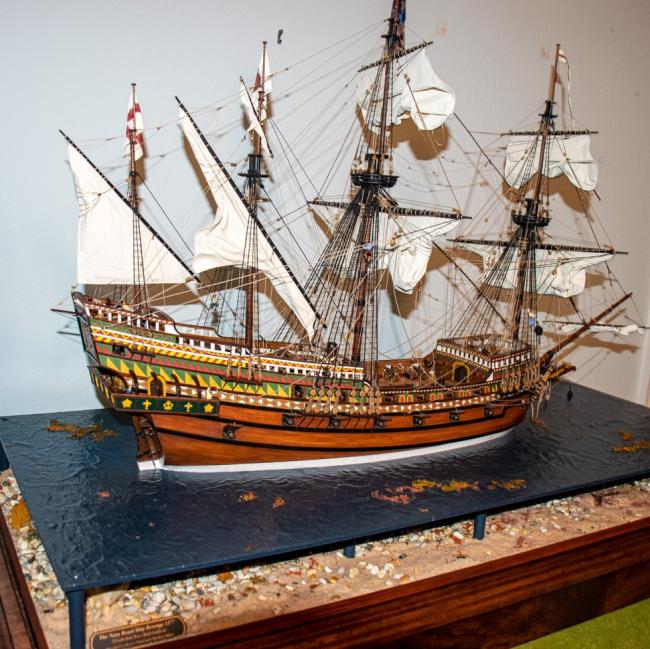
I ordered both of the above kits several years ago and as no ship has struck my fancy, I decided to give these a go. It's definitely different from what I'm used to. First chore was some supplies. I bought the recommended Rembrandt chalks, a variety of paints (I decided on Vallejo) and then spent some time on the internet matching the Foquil / poly scale colors to the Vallejo (VMA).
I plan to use both kits in one larger diorama so I will be completing as many of the structures from both kits before I try my hand out the layout. In this regard I have been following Grant's shipyard build and will likely use it a lot for reference. Unfortunately no such log exists for Foss landing despite the kit being over 20 years old. Hopefully I don't mess it up too much

. I am also using some of the wonderful posts in the techniques section. Karl's section on painting castings has been really helpful as has Dr grunge's wood clinic. So with all of this in mind, let's get started - Foss landing is first up
I won't bother with what's in the box and tools. If you are on this site you already know all the great stuff in the box.
First step is to prepare the castings - metal ones are supposed to be painted with earth however I used karl's recommendation and painted anything that supposed to be metal flat black. The resin castings were to be painted a variety of Floquil colors and again, using Karl's tutorial, I spray painted all the resin casting earth color. Since I was eager to see how I could do on the casting, I painted many of them almost to completion. here are a few examples
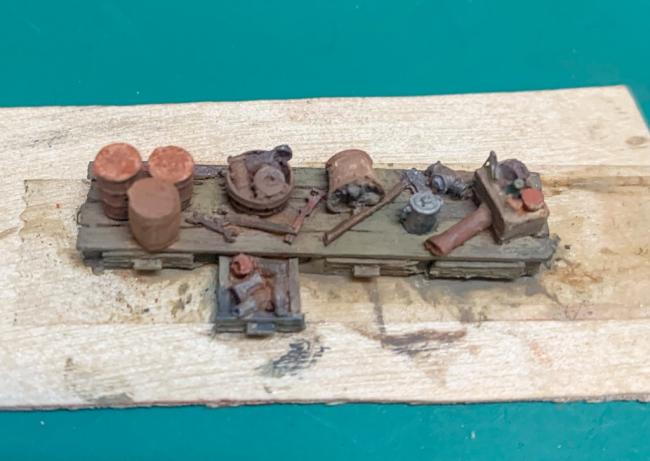
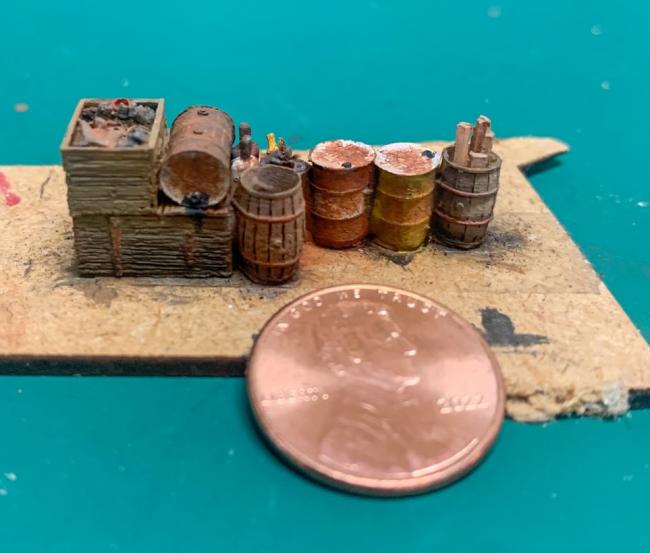
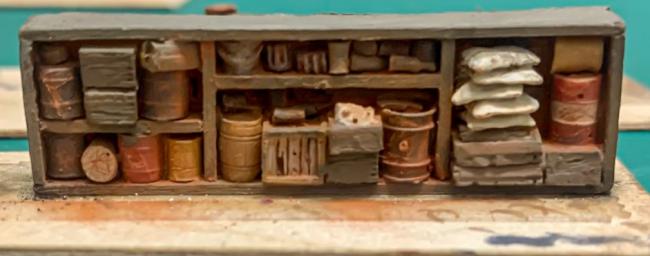
these were all put aside for later. There certainly are a lot of barrels and oil drums to paint!
The first structure in the Foss Clam and Oyster Co building. Unlike the shipyard building where most of the structure is built with individual boards that can be detailed, this kits' buildings have pre-made clapboard walls. Preliminary steps include painting of the shingle sheets, tar paper and window frames and adding texture to some of the stripwood. Most of the wood at this stage is for trim so other than some texture, not much else can be done as it is quite small.
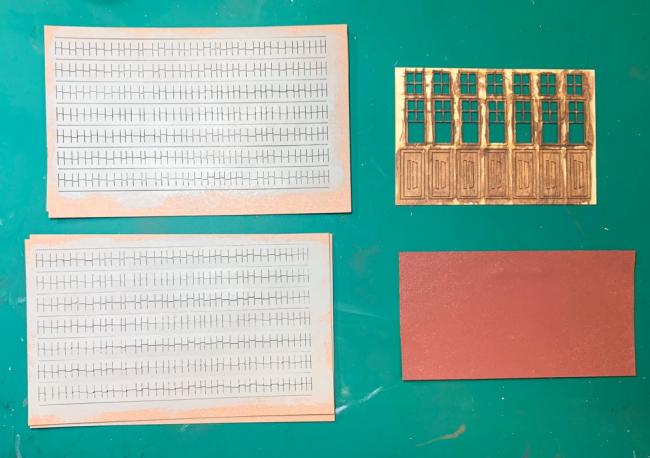
The clapboard walls are prepared next. First is with the wire brush to add texture, then fine nail holes along the walls to simulate where the boards are nailed to the underlying studs. Additional details can be added to show a variety of decay - using an 11 blade: some boards can be loosened, split cracked, warped etc. I did not want to go overboard here as these structures would be in daily use and not dilapidated or abandoned.
All of the wall are then braced with 1/8" sq wood to prevent warping when painting.
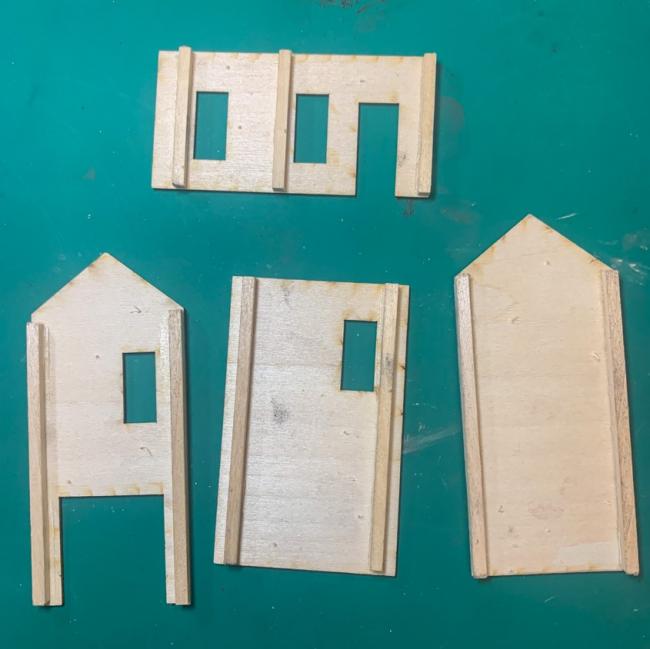
Unlike the shipyard, there seems to more painting with this kit. I will probably use chalk to do some of the weathering rather that the paints. Floquil grime is called for the base layer on the walls - I used Vallejo antique white. I noticed that the wood is quite porous so I had to be very light with the brush. before I put on the next layer, after the paint had cured for 48 hours I used a light coat of satin polyurethane to act as a sealer (here is the ship modeler rearing its head). The next layer is Boxcar Red (50/50 mix of VMA 71.038, 71.105). once dry, a light sanding with very fine sandpaper was called for followed by wall streaking with more paints. This last part I will leave until the roof and windows are on to get a better idea of where I want the streaks to be (and I may used chalks). Here are the wall to this point...
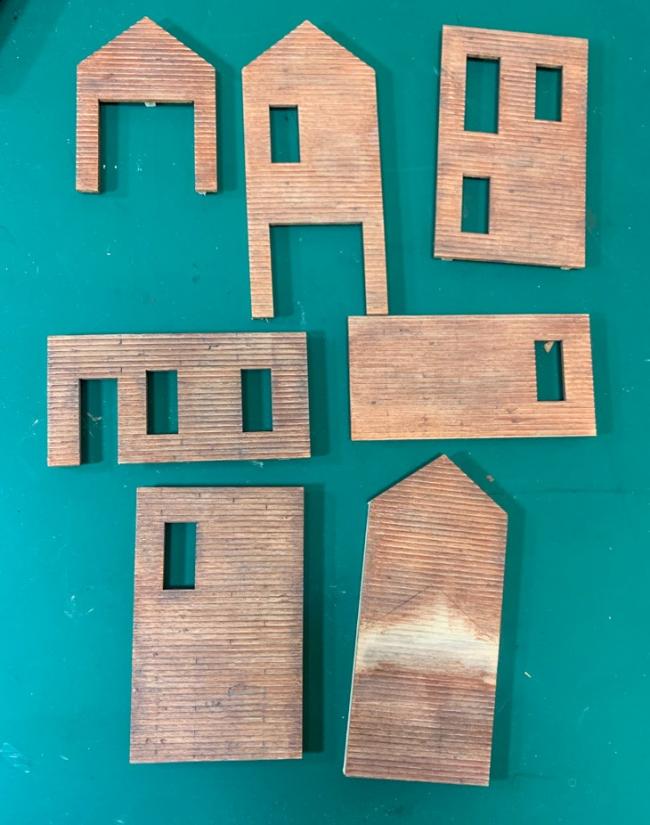
It's kind of hard to see some of the details (I even added in a few random knots) given the low resolution. After the walls were painted I grunged them up a bit with some grey chalk. I may use some black at the bottom when the structure is complete to represent more dirt and grime. If your wondering what's up with the wall on the bottom right, the lower part beneath the angled line will be hidden so I used that for testing colors and grunge.
And finally, while waiting for the walls to dry, work was begun on the windows and the clam and oyster sign. Each window has multiple parts including the inside frame, outside frame, lower sash, and mylar windows. These can be seen in one of the earlier photos. first they were treated with white paint to simulate peeling. I tried the terrycloth method as described in the manual but was not really happy with it. So I went with a stiff bristle brush (I think I read about that on the shipyard build). The frames are supplied with a sticky backing. Once painted, the mylar "glass" (which comes cut to size) is is stuck to the upper part of the inside frame. The outside frame is then stuck on top of the inside frame, which then fits into the window openings in the walls. I made holes in some of the window, took one pane out completely and took out just one corner in another.
.
the clam and oyster sign was fairly straight forward - 3 pieces of strip wood were weathered (thanks Dr Grunge!) and painted white with the bristle brush. They are then glued together and some nail holes added at each end. The dry transfer decal is now placed on the wood. I had no idea how this would work given the age of the kit (at least 7 years since I bought it. Brett has great instructions on how to do this. Not all of the deal transferred however I think this add the the ages look. The decal was rubbed with the end of a paintbrush to burnish it into the wood (you can actually see the wood grain through some of the decal). The a few very light swipes with the steel brush and it was done.
Here is a pic of a few windows and the sign...
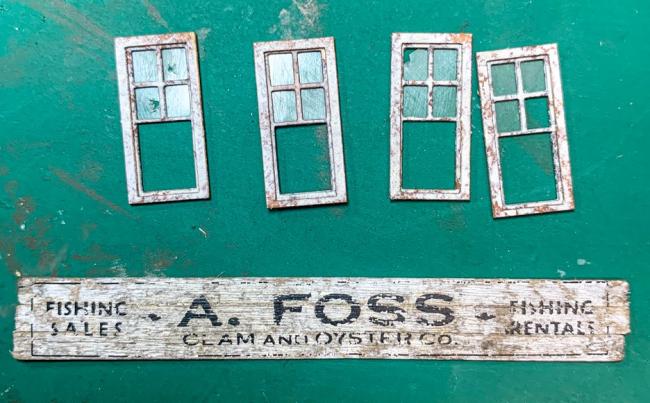
That's about where I am at currently. I think Ill try to post step by step in the future to keep things shorter. Any comments or suggestions are always welcome.
Jeff
Comments
Welcome to the forum, and, that sign looks perfect.
I'm sure you've noticed that this building also appears on the Shelby's diorama, which Ken has so exquisitely just completed.
We all look forward to following along as you progress and its great to see another ship builder joining us. Some of us just cant resist the waterfront, whichever genre we model.
Have fun, ask questions, but most of all, enjoy !
Your off to a fine start. Perfection on that sign.
What scale is that ship?? It's beautiful!!
Jerry
Jeff
that ship is awesome! i would never endeavor to build something like that. i would screw the rigging up so bad.......
Work continues on the Oyster Co. After the windows come the doors. 4 are cast and one is constructed in layers like the windows. The 4 freight doors were done in layers with the white applied to he wood painted a variety of shades with a hint of red as this was the original color before weathering. Similar process for the wooden door. rust added at hinges and doorknobs
Next several of the wal were trimmed, again using stippled white to simulate peeling paint. The bill of goods dry rub decal was placed at this stage. I did not know what to expect given the age of the decal however it turned out OK except for some missing letters at the top. Turns out dry rub decals don't last for years, a problem that became more pronounced for some of the smaller decals. The bill of good sign was then covered with a light coat of satin polyurethane to keep the letters in place (hopefully) and then dulled down a bit with grey chalk. Photo below shows the lettering before the grey chalk was added
Now the walls are completed by adding the windows with the lower panes and some signs to the back wall. One of the signs was the red coke button that required a Coca cola decal. Needless to say this did not work at the decal did not separate from the paper. I tried a few methods after doing some research but none seemed to work. So for the coke button, I found a similar sign on the internet and shrunk it to size and glued it over the button. Here is the result...
I think it looks passable. Next a few more signs were placed. The sign some on a paper sheet. The sheet was scuffed up a bit with fine sandpaper, cut out, glued and weathered with some chalk. Here are some photos. Note the installed windows: some propped open with a small wood board, others with wooden slats to cover holes and another with several boards through which a stovepipe will be placed. The boards were completed with some rusty nail holes at their ends.
The clapboard below several of the sign were weathered to simulate paint and rust coming off of them. Hopefully I did not over do it
And finally I think I may have found a way to use the old dry rub deals. Double sided Scotch tape was placed on a wood board and a single deal was cut out and stuck to the tape. The tape was then trimmed with #11 blade very close to the decal. When the decal paper was removed I ended up with this...
Although the tape is slightly visible in the photo, this is highly magnified and it is pretty much invisible and regular scale. I think this may allow me to salvage the rest of the decals in this kit although some have been ruined in my attempts to find a workable solution.
Jeff
Yeah, the lack of longevity of the dry transfer decals has really pissed me off for years. They worked great for about 15 years then pftttt. Once I learned of this limitation I immediately abandoned the use of them and went to laser cut paper stencils where applicable and possible.
A little dusting on those decals and they'll just bend in aged and beautifully.
Thanks for all the kind comments. I was a little apprehensive when I started these kits as the weathering process is all new to me. However, with some of the great tutorial posts here and Brett's wonderful instructions it has been easier than I thought.
Once the windows and walls are complete it's time for some window treatments - shades and curtains. Shades are simply black paper glued to the inside of the window. One window has curtains with part of it hanging out the open window. Much of this is unseen (though will stand out better if i decide to add some light to the structures. Next, the second story door and first floor wharf door are added. The previously prepared clam and oyster sign is glued and finally the walls are glued together. Much of this can be seen in some of the following photos.
A simple L square was used to keep things squared up.
The left wall awning over the freight doors is now installed. This was painted earlier. Instructions called for some testors Dull Coat and then bush with some rubbing alcohol to fade it. However, I did not want to buy any more supplies at this time so I decided to try what i had on hand - matte finish polyurethane. I then painted some alcohol on it after the polyurethane had dried and this was the result...
Before:
After:
I think it is acceptable. The awning is made by cutting strips and gluing them onto a thick template with some overhang on all sides. I left a bit more on the back side as this would be against the structure.
The awning was weathered with a variety of chalks (grey, black, white, rust) then glued at an angle against the building. Two wires are added to simulate support. I mixed some black grey paint with glue and put it around the areas the wire contacts the building and awning to simulated caulk or tar that might be found at the ends and some black chalk to stain the canvas below the points of attachment.
Before starting on the stairway and landing to second floor, I added some supports to in inside tall wall that will give more support to the roof when attached (red arrow). The other red arrows at the corners of the first floor of the building demonstrate where I added wood the side walls so that they would have more surface for glue when attaching them to the front and middle wall.
Now for the landing and stairway. Construction was straightforward. All the wood used was to be treated with white paint to simulate peeling however I left the landing floor and steps in the natural faded wood condition. I figured one would not paint the steps and landing as they may end up slick. Templates are provided to allow one to make the construction pretty full proof. Here is the landing:
However, one caveat: The landing has 2 supports. A template gives the dimensions and angles to cut however the if you follow them template the supports, which should attach to the building just above the window, will end up a good distance below. See next photo:
In this photo, A should equal B but B was at ~3.5 mm longer. I was an easy fix and here is the final staircase and landing.
I added some nail holes and rust to the landing boards but not the steps. That whole structure is much too delicate and I did not want to mess things up for a relatively minor addition. I also used some black / grey chalk on the stairs and landing to simulate use where steps would be taken.
Next up is the roof
jeff
The staircase is very nicely done and the peeled white everywhere matches the age of the structure.
One suggestion I would have is to pull out one of those black window shades you have, they will just disappear when the roof is on.
Pull one out and replace it with a light grey, stipple on some chalk to give it a random grimey look.
Put a piece of paper over the structure as a false roof to block the downward light and see if you like the grey better.
It's an easy quick test to do now before you get the real roof on.
Everything is looking good.
Karl: I tried to pull off one of the shades but the paper started to rip. Rather than mess something up or try to use some sort of solvent to dissolve the glue, I think I will try your suggestion on the other main building in this kit.
Jeff
I am using non water soluble gorilla glue. Not sure what would loosen this but so far I like how this glue sets - does not take as long as white glue or what I've used on my last few ship models, Weld Bond. With ships models, you ofter have to debond glue to fix stuff like beams and planks. Water is not good as the wood will swell. Weld Bond loosens up with alcohol which does not change the wood. For this project, I don't think changing the shades to a lighter color is that important so for now Ill leave them as is and try Karl's advice on the other buildings. Thanks for all the helpful advive though.
Jeff
Onto the roof. The simulated tiles / shingles were painted earlier and now are repainted with black and grey to produce a variety of shades. Here is one example:
Next, the edges of the template and some of the bottom was painted green. The individual rows of shingles are cut from the sheet and applied to the thick cardboard template. Lines are drawn on the template to keep the rows lines up. Here are a few rows already glued...
And here is one roof complete except for the cap shingles:
The hole is for the chimney. Rather than just glue the chimney to the angled rood, I drilled a 1 mm hole in the chimney (metal was fairly soft) and stuck a 1 mm brass wire in it. on the opposite site of the roof, I glued a small 1.5 mm plank to give more purchase for the brass wire...
The capping shingles are made from the unused perimeter of the shingle sheet. Instructions said to use one large sheet but I cut them down to size and applied them in an overlapping fashion. Here are a few pics of the 2 finished roofs. Also added are the stove pipe coming out of the window and the chimney. The chimney was first painted with VMA aged white ( 71.132)and then dry brushed in several layers to paint the bricks using VMA 71.105 (this is listed as brown but look more like brick red) . Support wires were added to both.
Some soot was added around the chimney and streaks added to roof. The "tar" around the base of the chimney is glue mixed with some VMA black green (71.021) and black. I also used some aged white to add some bird dropping to the roof. hard to see in the photos however. After hanging the 4 freight doors this structure will be done.
Jeff
They 'almost' look like individual shingles, very nicely done.
The brick chimney is a masterpiece and came out extremely well.
The whole structure looks great. Very well done.