After much thought and contemplation I have decided that the BlueSky Company Warehouse will be my next build.
The things that draw me to BlueSky, other than the wonderful design and story here, are the wonderful modelers that have worked up BlueSky such as Brian Nolan, Mike Chambers, Dave Revelia, Karl Allison, Kevin O'Neill (Karl and Kevin had a big part in the O Scale Pilot Model I believe). These are just the ones I know of as I'm sure there are many more. Its also, as everyone knows, Brett's first SWSM Kit. I think it would be awesome to build this early kit incorporating the newer techniques that Brett has developed since BlueSky. In addition, I feel it a tribute to Brett and SierraWest Scale Models to bring this classic kit to life once again.
Unlike an official forum build like O'Neills, I will not be posting each and every step as I work through this wonderful kit. Rather I'll post progress photos and field questions and comments, if any, as I move along. My progress here is predicted to be slow as I am focusing my attention on the wood clinic and a few other projects. I will likely incorporate some features of the O Scale version and will point those out as they materialize. Would enjoy hearing from those that have built BlueSky and look forward to working through this build.
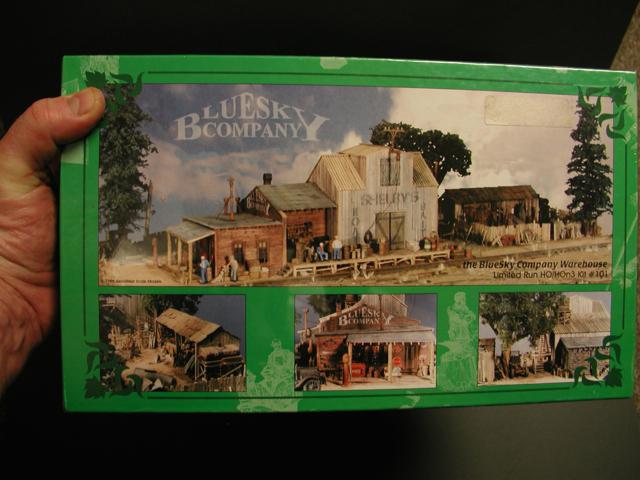
Brett's first kit and his famous green box that started the SierraWest Scale Model legacy...
Comments
I'm holding it right now Ed! Thanks for your support Ed and aim to do this kit justice as I feel every SWSM kit deserves, and that is our best efforts.
Carl
Geezerbill
I was thinking about doing BlueSky along with you I was just wondering do you and I have the same run.
Then I thought about Eureka Springs Engine House still trying to decide what to do, Then there the Logging Camp Essentials would kick start my layout with the mill.
Help me decide.
Thank's Carl
Carl
Wes, I was meaning to ask you about that. Thought I may have seen your build of the O Scale BlueSky somewhere before, but before I decided to work up my HO version. message me about where you posted your build...glad you'll be following.
Im so bummed I never got to finish. If the rand dollar rate ever gets better, id love to get my hands on another.
First step in any classic or otherwise SierraWest Scale Model kit is to open the box and see what we've got!
After the protective wrapping was removed the box was opened...shot of the paper packing still in its original position...
I was first greeted by the holy grail of each SWSM kit...the bible...oop sorry...manual. This was ceremoniously removed and carefully set aside for attention later. The box must be inventoried for completeness being purchased on the secondary market as there is always that chance something was removed and not put back in the box...a risk worth taking on these classic kits.
With the manual safely set aside the remainder of the contents are ready for inspection.
Ah...ha...gotcha! thought I'd go right for the casting didn't ya? Remember I love working with the wood so that's the first order of business. Bags 1-10 of clean, sorted, labeled, and actually some pre-cut stripwood and scribed siding.
OK...now the castings. In discussing a bit of the history of BlueSky with Brett, he explained that it was quite the event in the modeling world to have a craftsman kit with all resin castings. Modelers were a bit jaded by the poor quality resin castings up to this point. However, Brett set the standard for resin castings with BlueSky and never looked back!
As I work through this build I will feature some of the individual castings. So, on we go to step number 2...as follows...
That's right...you knew step 2 already...
Your point is well taken and one of the reasons I decided to build Brett's first kit. As you know, I just completed his newest kit, O'Neills Fabrication and look forward to building this classic kit, taking into account the knowledge of the newer techniques. Brett's casting philosophy has evolved over the years to that of a finely tuned machine! I'll tell you though, those resin castings from 1995 are as crisp and clean as they can be. Back to that wall that only has 7 boards on it over 3 nights work! You'll see why later on...
I started with the front of the barn and after detailing my stripwood, began laying out the wall. The entire bottom of the front wall is covered by a loading dock so my treatment of the board ends along the bottom front are minimally detailed (i.e. won't show).
The barn front wall with my stripwood "hung" about half way. I also started the left barn wall and the loft rear as shown. Brett utilized the ingenious "stripwood traps" from his very first kit here that provide a near perfect corner where two walls meet.
The Barn is the original structure of the BlueSky Company Warehouse complex. As such, I wanted the barn to be fairly weathered. Not beaten down just well worn and minimal repairs. Since Brett sold this kit, albeit 22 odd years ago, it's mine now! As a result I decided I wanted some heavily weathered areas mostly in the corners where a gutterless roof would allow water and rot to take hold. But only at the bottom, the rest of the structure will be in reasonably good shape. I love the look of rotten damaged boards near the ground with the original framing peeking through. You know the look I'm sure. The stripwood over card stock makes this a bit of a challenge. So, I carefully laid out my side wall and at the corner cut out a chunk of the card stock and added a section of framing (see figure 1). This would allow me to detail the board ends and allow the simulated wall framing to show through.
(figure 1) Note the stripwood framing spliced into where a piece of the card stock template was carefully removed.
I then proceeded to layout my detailed strip wood for this corner (figure 2). I will have something similar in a couple other corners but not as significant as this one. Although it appears large...I guess...it is not in a highly visible area and will be one of those nifty details that you have to look for!
(figure 2)
Note the framing peeking through the siding. The black paint along the bottom edge serves to hide the card stock template where my detailed board ends may gap, have small missing pieces, etc..
More later...