Hello all,
I've been a member here for a number of years, but this is my first actual post.
I am not what you might call a “trains” guy – more of a “sticks and strings” guy. Most of my modelling to date has been of ships, specifically 18th century sailing ships. A few years back, I came across this kit by accident when a fellow ship modeller posted something about it on the Model Ship World (MSW) forum. I can’t remember now exactly who that was, but whoever it was, it’s all his fault!
I thought this was a lovely diorama – something I had not tried my hand at before, and even though it’s not something I would normally go for, I was intrigued to learn more. My investigation led me here to the SierraWest website, where I learned that this model kit uses a number of interesting and innovative modelling techniques that are certainly new to me. I just had to give it a try. And while I was at it, I couldn’t help myself and bought a “companion” kit of Foss’ Landing – something for a future build…
When I broke the kit out the other day, I was thinking it was only a couple of years ago that I had bought the kit(s). When I thought further on this, I realised that it was actually in 2015 that I bought these, fully intending at the time that these would be the “next” model. Well, seven years later, I’m finally ready to start!
I’ve decided to post my build here in the hope that all of you who are experienced with these excellent kits might guide and advise me along the way. All comments/constructive criticism are welcome.
Let me say up front that I’m very impressed with the kit contents and especially the detailed instruction manual. I’ve also seen the videos here in the “University” and have read through some of the many build logs as well.
Advance Preparations
Construction begins with some advance preparations. As this is an older kit, there is reference throughout the manual to Floquil paint colours. Now that these have been discontinued, Brett states that he now favours acrylic paints from AK Interactive. However, there is no direct conversion suggestion from named Floquil colours. I spent a considerable time researching on the internet to try to get as close a match as I could to the Floquil colours. Try as I might, I could not find a conversion chart that included both the Floquil and AK paints. I ended up using a site that specialised in paint matching, typed in the Floquil colour name and then used the resultant screen depiction to try to match against an AK colour. Although there are certainly limitations on screen/monitor colour representation, I think I got reasonably close in the end. At the end of the day, I guess an exact match isn’t important, but I’d like to be “in the ballpark”.
Three Floquil colours are needed for the advance preparation: Grimy Black, Boxcar Red, and Earth. My AK matches of choice were Basalt Grey, Mahogany Brown, and Grimy Grey respectively. Why paint manufacturers use obscure names instead of a scientific identification system is beyond me!
First up, Bag
#5 is called for:
From there we are instructed to extract the three sheets of 4” x 6: tar paper, the laser cut sheet of awnings, and the sheets of laser cut shingles.
The three sheets of tar paper are all sprayed with a coat of Grimy Black/Basalt Grey on one side. One sheet has the same on the reverse, while the other two get a coat of Boxcar Red/Mahogany Brown.
The laser cut sheet of awnings gets the same treatment, and the laser cut sheets of shingles get a light coat of Earth/Grimy Grey – “just enough to hide the white paper”.
This was my first experience of using AK Interactive paints, so I was somewhat apprehensive about leaping in. My research suggested that for airbrushing they should be reduced with AK’s own thinner at a ratio of about 70/30 thinner to paint. So that’s what I did. I took a little while to do some practice and fiddle with air pressure and paint delivery. With the air pressure dialled down (about 15-18psi) and the paint delivery shut almost right down, I was pleasantly surprised at how well it sprayed, with absolutely no tip-dry occurring. Here’s a picture of the completed painted parts. I’ve turned one sheet of the shingles over to show the original state. I’m pretty happy with the colours as they’ve turned out.
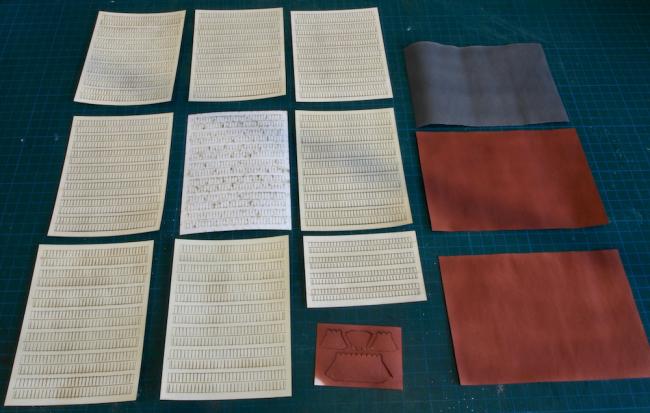
The other advance preparation was to make up an alcohol stain using non-waterproof black ink dissolved in isopropyl alcohol at a ratio of 1 teaspoon (5ml) of ink to one pint (600ml) of alcohol. I took Brett’s advice and ordered the Higgins brand of ink via Amazon.
Okay, we’re off and running – or crawling, anyway!
I have one question at this point. In the first picture above, of the contents of Bag#5, at the top left of the picture is some corrugated metal. I have read through the entire instruction book and looked through logs but cannot seem to figure out what this is for. I'm sure I'm missing something as I read. Can anyone enlighten me please?
Grant
Comments
Thank you for taking the time to explain your processes and steps thus far.
I can already tell that this is going to be a great and informative build thread.
As far as I can remember, but I'd have to check, the corrugated is for the shed roof where the boards are cut to length before going into the "steam box" .... I'll go see what I can find out for you ...
This is where the planking for the hull and decking is cut to length before being placed in the steam box so that they can be bent around the the hull 'skeleton'.
It has a corrugated roof.
Hope this helps.
It looks like Ken already posted and gave you the answer while I was still 'slow' typing, good to see though that we're all on the same page.
- "The Dr Grunge Advanced Wood Clinic" by Ken Karns,
- "Painting those Details - The Basics" by Karl A., and
- "Advanced Painting and Weathering of Details with Kevin O'Neill", curated by Karl A.
There are many more but these to me are all seminal works - so much so that I have taken the liberty of copying the content (minus other comments/questions) into separate documents that I have now printed in hard copy as a handy reference while I work. I hope my doing so does not breach any forum rules - please let me know if it does.
I'm a fairly methodical person, particularly when it comes to doing something new, so I'm working my way through the instruction manual page by page. Page 4 is all about Chalk Sticks/Pastels and preparing an initial two palettes - one of "wood" colours and one of "rust" colours. At some point in the past, I must have read through the manual, the list of supplies, and the various pieces of advice here in the forums on the different colours/shades/tints needed as I seemed to have quite a few. Inexplicably, I seemed to be missing a few key ones, so promptly ordered more. I have now amassed quite a collection. I decided that it might be a good idea to make up a ready-reckoner colour chart.
Brett advises making up these two palettes in advance, a trip to my local Spotlight (sewing/craft) store produced this:
This version has 30 separate containers, each with a screw-top lid. By happy coincidence, that is the exact number of chalks that I have (so far!).
Brett advises creating the powder using a single edge razor, but in the same thread by Marty, he showed the use of a bastard rasp for achieving this a lot more quickly. So I thought, what the heck and followed suit.
By doing this over a sheet of paper that had previously been folded to create a pouring funnel, the job went quickly and easily. I took care to wash/scrub the rasp between colours so as not to cross-contaminate them.
Brett specified the colours for the wood palette as 408.3, 408.9, 409.3 and 100.5. However, for the rust palette, he simply says to use one medium orange, one medium red, one dark red, and a cool grey. Okay, first time to make some choices - scary.... My selection for the rust at the moment is 235.5, 370.5, 372.5, and 727.7. If anyone thinks these are a poor choice / the wrong choice, please speak up - it's literally five minutes work to change these.
Here are my two initial palettes - the wood palette on the right, and the rust palette on the left. Each jar contains about 1/3 to 1/2 of a chalk stick.
All of the jars have two labels on them - one on the lid and one on the body - to ensure correct identification. I went ahead and labelled the remaining jars while I was at it and will fill them with pigment as/when needed. So here is my "ready use locker" ready for action.
Next up will be preparing the strip wood siding for the main building.
I'll have to see if I have a shipyard manual around here to check, but, I'm kinda concerned about reading that you scraped the chalks into containers, that doesn't seem right to me and I can't imagine it being in one of Brett's manuals as that is not the way the techniques work.
I'll check up and get back to you before I post anything else.
Looking forward to watching your progress Grant, you are definitely focused and organized.
411.3 is also my 'goto' Tom, 95% it is always that one.
I'm still a little confused and have emailed Brett separately for further clarification.
http://www.craftsmankituniversity.com/vanforum/index.php?p=/discussion/800/the-dr-grunge-advanced-wood-clinic/p1
I guess the first thing to get one's head around is that this is a multi-step process and both Brett and Ken make that clear. So here I am starting with Step 1 - applying the initial texture (or "wood graining" as Ken calls it).
For my initial attempt at this, I used a brass wire cleaning brush (obtained from the local hardware store) pictured below. In this picture I'm showing the back side of the batch of strips prior to brushing. I took the precaution of marking a line across the grain to indicate the "back" side and to help me identify which side is "up" as we are only texturing one side of these strips (per the instruction manual).
Following Brett's advice, I did this task in batches of five strips at a time. Here is the result after brushing.
Despite the amount of "shavings" produced, I was not particularly satisfied with the result and decided that a more aggressive brush was required. This is the brush I used for the second round.
It is actually a File Card (used for cleaning the scarf from the teeth of files). The teeth are steel and quite hard. I found that around five to six firm strokes with this brush were enough to impart a more grain-like texture.
To provide some greater contrast, here is the same batch at the same stage on a black background.
In the above picture, you can clearly see the amount of "fuzzies" left behind. I followed Ken Karn's advice for cleaning these up by drawing each strip through some 0000 steel wood, first with firm pressure on the edges, and then with light pressure on the face. Here is the result after this initial cleaning up.
This has removed around 90% of the fuzzies, which should be sufficient for this stage.
Before I proceed to the next step of adding some initial colouring to these strips, I'd appreciate any input/opinions/further guidance on whether I have achieved sufficient "graining" at this point.
Grant
In the Instruction Manual, Brett says to use 408.3 only at this stage, although he then adds that while the boards are still wet, to scrape a little white powder on top to "grey" it up a little. On the video here, Brett demonstrates using three different shades of brown to provide some natural variation.
To further confuse the matter (for me at least), later on we are told (at the point of fitting the individual boards) to apply a light wash of black alcohol stain to dampen the boards and then blot (with a dry brush) some grey, white, and/or dark raw umber powder on top.
I get why we do this latter step, but I'm confused about the initial step - should I just be using the one shade (408.3) per the Instruction manual, or all three shades per the video?
Or am I over-thinking this and it doesn't really matter, coming down to "modeller's choice"?
May I suggest you experiment with different techniques and find which one you like best. There is usually extra strip wood included in each kit to allow for some experimentation. Through careful use of cut off board ends I usually end up with extra wood with each build. Let the process be a fun experience. There is no right or wrong process it is a matter of personal choice. It's all about having fun!
The chalk will colour any 'white' wood you use in the the same way as the wood in the kit. It's a great way to learn and observe how much (little) chalk is needed, how to wash it in with the alcohol, the different effects you can get and numerous variations. Once understood how and why it works the technique is incredibly versatile.
Grab some cheap wood coffee stirrers or popsicle sticks from the grocery store and have some fun !!!
Practice, play and enjoy.
After graining and prepping the wood, put down two strips of double stick tape and lay out your wood. As Brett and others have illustrated, you can use several different shades of chalk and randomly scrap over different sections of the wood. You don't need as much as you think. The alcohol brushing blends the various chalk tones while providing variability both within an individual board and across the boards. If it's too light, you can always add more chalk and brush again with alcohol.
Take Karl's advice and try the different techniques on coffee stirrers or any other plain sticks. This will give you the chance to experiment and stay relaxed without worrying about the kit. There is a real freedom in trying the various chalks individually and in blending them across the boards.
The great thing about it is that wood weathers in all types of shades. There is no wrong answer. Most of all, Have Fun!
I spent today in the “big” workshop, progressing a furniture project I have on the go but nearing completion. I’ll get back to this build tomorrow and start experimenting - with freedom!
So today I broke out the popsicle sticks and had a little play, including testing both the preferred/suggested method of applying chalk directly over the wood, and also from some of the pre-prepared jars. None of you will be at all surprised to know that I quickly came to the conclusion that not only was the suggested method a lot easier, it was also a lot quicker and offered far greater control. Sometimes, you just gotta learn the lesson for yourself!
So having gotten over my sheer terror at trying something new, I then did a small batch of my grained kit wood. I've paused there briefly to seek some feedback from you all on the level of colour I've achieved here. I was still a little apprehensive as the manual says, "since you can wash excess powder away don't go too light on the powder", while on the video, Brett emphasises that "the number one mistake most beginners make is to use too much chalk and not enough alcohol". I used the pictures in the manual and on the video as a guide to how much chalk powder to use, and applied plenty of alcohol, trying to replicate what I'd seen Brett do on the video. The instruction manual also tells us that once we've brushed in the 408.3, to then scrape a small amount of white powder on top to "grey" it up a bit. I did this, and brushed it in again with more alcohol.
My concern is that the boards might now be too light. I'd value some opinions here - do they look "about right", or do I need to go over them again with more 408.3?
An overview of my "test" batch:
And a macro close up:
However, if you wanted to tweak it some you could modify the darkness values of some of the boards. In the picture, they all appear to be close in value (darkness). If you wanted, you could take a few boards and add some more chalk to develop a medium value. Then a very small batch and go a bit darker still. It would have to be subtle so you don’t create a zebra effect with the final siding. Again, that’s just an idea. The boards look great the way they are.
One of the advantages of scraping on the chalk over the boards, the effect naturally creates different colorations based on powder concentration in the various areas of the boards. As you weather more boards some of this effect will happen naturally.
I’m so glad you got started. I’m really looking forward to your build. Don’t forget to have fun on the journey. Great job!