I'm starting this thread to describe how I find, size, print and apply the labels I use on the incredible SWSM castings and detail parts.
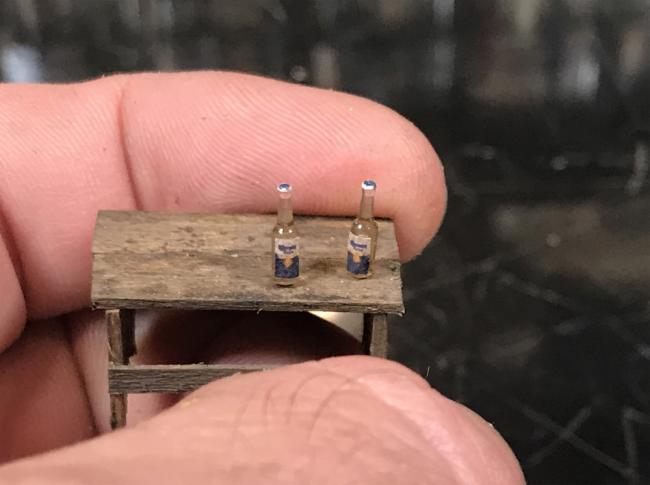
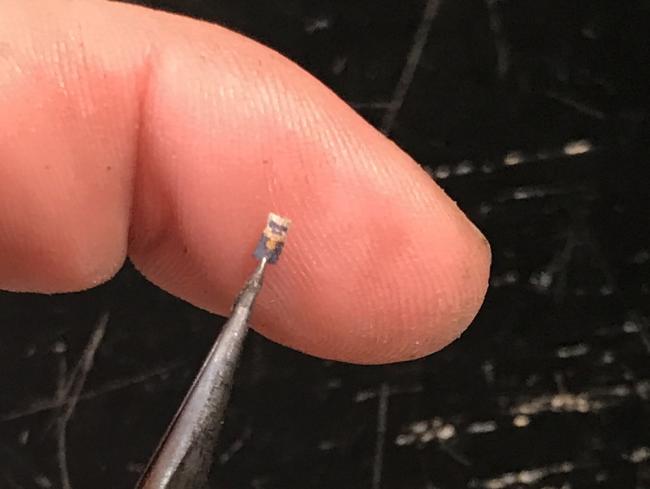
I use a low grade 7 year old inkjet printer that cost 49.99 at the time and Photoshop 5.5 from 1998 or so that was free, so, no special equipment is required. Any standard printer and image software should work fine.
I'll do a basic overview shortly and then get into more detail through out this week.
Comments
Terry
By the way how many of those little bottles does it take to quench your thirst??
Jerry
Thanks guys,
here is the basic list of the steps I take to produce the labels. I'll do a step by step with screen shots in a couple of days next time I make some labels.
After that I'll do a process on application.
First find an image of the label that you require and save it to your computer. A google image search will usually provide plenty of results to choose from. Such as "Acetylene tank labels"
1) Open a new sheet in your graphics program. make this sheet 3.5"x4.5" at 1200dpi (400dpi will be fine for most things, start there)
Slide this into the background for use later.
2) Open your downloaded image. Look at the properties, most are 72dpi, change this to 1200dpi (400dpi will be fine for most things, start there)
3) Select only the area of the image you want to print and copy it to the clipboard. now minimize this original image out of the way.
4) Click 'new' again, the new image dimensions should automatically be the same as the image you have copied to the clipboard. Make sure the dpi is 1200, this is important !
4) Click 'paste' to import your saved image, it should fill the new box.
5) Measure the area on your detail where you want the label. either the width or height, I generally use mm as it's easier for me to work with on the tiny labels.
6) Now, go into the properties of your image and change the print size to what you require for the dimension you measured, ie width - 4mm. Ensure the dpi remains at 1200 (400dpi will be fine for most things, start there) and you check constrain proportions. (This will mean the second dimension is changed automatically for you and the image proportions will remain the same.) Save this image.
7) Choose "select all" and Copy this resized image to the clipboard.
8) Go back to your original 3.5x4.5 blank sheet and paste your saved image there as many times as you need. Save this sheet.
You can now repeat the process from steps 2-8 with different labels to fill up the sheet or just go ahead and print if you have all you currently need.
If you have made sure every step is at the same 1200dpi (400dpi will be fine for most things, start there) your labels should print perfectly.
SAVE YOUR WORK OFTEN !!!!!
Next phase, 'advanced' options of what you can print on and how to apply to the detail.
I also have an old copy of Photoshop and Illustrator.
Will experiment with labels.
Keep up your great work my friend!
Pappy
I keep editing the first post ( about 30 times now, ha ) but I think I've got it pretty clear now. So, I guess I'm going to leave that post alone now and move on to the next post.
But if anyone has any questions just ask away, even if it's 5 or more years after this thread was originally posted.
Next phases/posts will be, 'advanced' options of what kind of papers you can print on other than regular copy paper, including Rizla... !!
How to do it, along with the pro's and cons of each type of paper.
If there's still interest after that I'll outline methods of how to apply your printed labels to the detail part to eliminate visible edges,
or wall if you are printing signs instead of labels.
I'd completely forgotten that I used to print on Rizla papers, until I just typed it in the previous post.
I should have used my method for doing that on my recent acetylene tank labels in the 3D Parts thread, they would (hopefully) have looked so much better.
I'll take pics as I redo the acetylene tanks in the next day or two and post them here...
Terry
I'll show you how to get them through the printer later.
It's basically the same as my method to print on tissue paper, but the benefit
is that the ink doesn't bleed hardly and you can get a sharper print, great for
labels.
I just started individual shingling a roof panel and don't want to stop halfway through.
I need a super thin sign for one of the builds I'm working on so it's a great time to explain/describe how to print on paper so thin that some couldn't imagine getting it through a regular printer.
Pics of my process and a description in the next post on how to print on...
tissue paper
newsprint paper, and...
rizla's (cigarette papers).
Despite the fact that I am printing a wall sign in these images, the basic process is the same for labels.
Firstly, my definitions...
Tissue paper - the paper that you get covering the acetate sheets we use for windows to protect them in our SWSM kits. Gift wrapping 'tissue paper' is probably the same, but I havent used it.
Newsprint - that really thin paper Brett puts in the boxes as packing to stop your kit box sliding around in the USPS box.
Rizla's - Cigarette rolling papers... Unfortunately, this is the only one that Brett doesn't provide, so you'll need to get your own.
Uses...
Tissue paper usually absorbs the ink and bleeds, so, is best for larger, low definition wall signs with less detail that you want to really 'snug down' to the wall.
Newsprint is great for high detail wall signs and labels, the edges are super thin for labels (but still need some work, to be described in a future post), also great for signs you want to conform to a clapboard wall.
Rizla's great for medium/high detail on labels or small signs. It bleeds a little but is really thin.
Pictures and process to follow.
I wanted a really worn sign for one of my current builds to go on a weathered wall and blend in completely. The thinnest and best material for this I've found is 'tissue paper' because the sign is aged, low detail and just letters some bleed/blur really isn't an issue.
Sized and scaled to fit where I want it.
I have a ton of 4x6 photo cards that used to come with my inkjet cartridges, I would have preferred cheaper cartridges at the time, but now I've found a use for them.
Step one, print your (sized/scaled) image onto the base paper, in my case the card, but use whatever you usually do.
Cut a piece of your super thin paper to cover the print, with a little extra. In this case I'm using tissue paper, but it's the same process for newsprint or a Rizla, or...
Use some scotch tape to fix it down so it doesnt snag in the printer. I usually do the top first, then both sides and I dont bother with the bottom.
Make sure your thin paper is smooth and flat.
Don't put tape where you are going to print.
Put your paper/card back into the printer, making sure the orientation and way up is correct. Reprint your image.
The image should reprint exactly where it was before, but now it will be on your super thin paper.
Cut your sign / label from the backer sheet , then cut it to size and apply it to your wall, detail part or where ever its final desination is.
Application tips and tricks will be in the next installment.
Terry